Flexible Printed Circuit Boards
Film coating system for single or double-sided copper metallization
APPLICATION
Smartphones and other mobile electronics not only have to be powerful, but also very light and small. However, wiring carriers are still needed to connect all the sensors, microphones, cameras, loudspeakers and computing units in the smallest of spaces. These modern devices require printed circuit boards in the form of thin films, as these are small and light and also adapt to the geometries in the housing instead of predefining them. It must be possible to solder the components to the PCBs, and these soldered connections and the adhesion of the conductor tracks to the film must hold reliably even with the smallest structures.
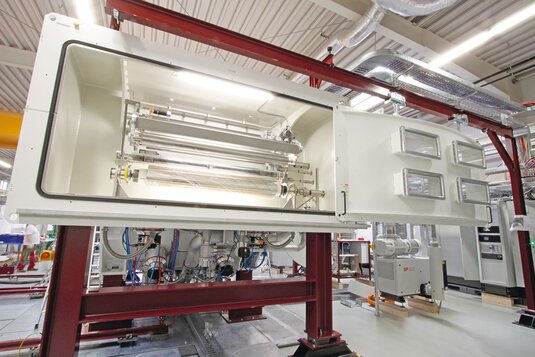
REQUIREMENTS FOR THE SYSTEM
The production system will coat the entire surface of up to 5 km long and 1600 mm wide films just 12.5 µm thick with copper using a roll-to-roll process. The galvanic reinforcement and structuring of the copper layer are downstream processes. The system must first remove residual water from the film by heating the film under vacuum. An adhesive layer must then be applied, which must be free of chrome for environmental reasons. Thereafter, there is the copper layer, which is over 100 nm thick. The system must be able to be evacuated again quickly after changing the film rolls in order to lose as little time as possible.
- Flexible and lightweight
- Reliable even with the smallest conductor paths
- Soldering on the circuit board must be possible
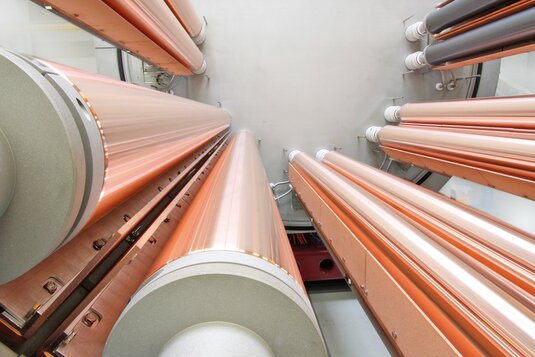
SOLVING THE REQUIREMENTS
FHR.Roll.1600 consists of separate chambers for unwinding, heating, coating and rewinding. The winding unit, therefore, remains in the process chamber, while the process units – namely tubular cathodes and heating plates – are moved out to the side on large carriages.
THE SPECIAL FEATURES OF THE FHR.Roll.1600
- Valve-separated winding chambers enable short times for substrate changes thanks to short pump-down times
- Film drying within the system
- Highest material utilization and longest target service life through the use of tubular cathodes
- FHR’s proprietary shift system
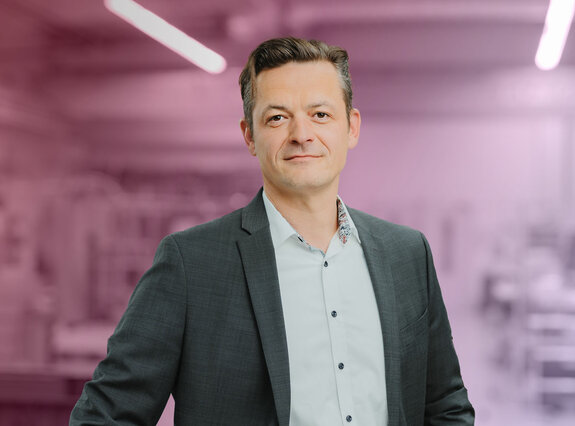
Your Contact Person
Do you have any questions?
Would you like to know more about our FHR.Roll product range? Our expert, Sven Häberlein, will be happy to help you. Get in touch with us.